Hey there, concrete enthusiasts! Have you ever wondered about the optimal time to cut control joints in a freshly poured concrete slab? Picture this: you’ve just finished pouring a smooth, pristine slab of concrete for your dream patio or driveway. The last thing you want is unsightly cracks ruining your hard work. That’s where control joints come in – they’re like the secret superheroes of concrete projects, preventing cracks and keeping everything looking sharp.
But when is the best time to make your move and cut those control joints? It’s a bit like picking the perfect ripeness for a fruit – too early, and you risk a messy outcome. Wait too long, and you might end up with a less-than-desirable result. Timing is key when it comes to control joints, as cutting them at the optimal moment can make all the difference in the longevity and appearance of your concrete slab.
In this blog, we’ll delve into the importance of control joints in concrete slabs, why timing is crucial when it comes to cutting them, and how to determine the optimal moment to make those cuts. So, if you’re eager to learn the secrets of ensuring a flawless concrete finish, buckle up and let’s dive into the world of control joints together!
Understanding Control Joints
So you’re pouring a concrete slab, and you’re wondering about control joints – when should you cut them? Control joints are like the safety valves of your concrete slab, helping to control where cracks might form as the slab cures and settles. It’s important to cut control joints at the right time to prevent unsightly cracks from ruining your hard work. The best time to cut control joints in a concrete slab is typically within the first 12 hours of pouring while the concrete is still plastic and hasn’t fully hardened.
This timing allows for clean, straight cuts that guide the natural cracking process along the joints you’ve created, rather than randomly across the surface. Remember, it’s better to be proactive and plan for control joints than to deal with unsightly cracks later on. So, roll up those sleeves and get cutting for a smooth, crack-free finish!
Definition and Purpose
Have you ever noticed those neat little lines running across the concrete floor or walls of a building? Those are control joints! So, what exactly are control joints and why are they important? Well, control joints are intentional breaks made in concrete or masonry to control where cracking occurs. Think of them as the seams on your favorite pair of jeans that allow for movement without tearing the fabric. These joints help to relieve stress caused by the natural expansion and contraction of materials due to temperature changes, humidity, and other factors.
Without control joints, the concrete or masonry would crack randomly, leading to a messy and unstable structure. In a nutshell, control joints serve the purpose of maintaining the integrity and longevity of a building by directing where cracks should form in a controlled manner. So, the next time you see those lines, remember that they’re not just for show – they’re keeping everything together!
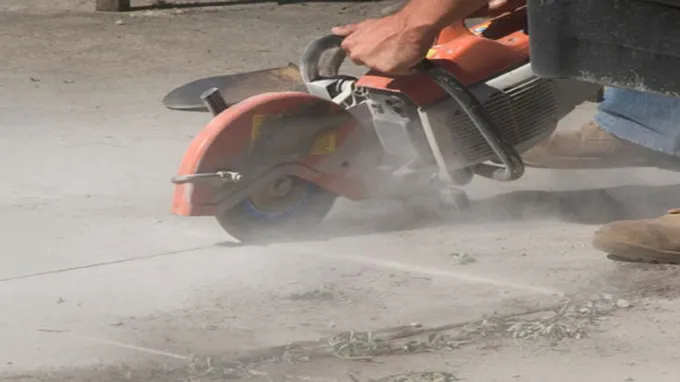
Benefits of Control Joints in Concrete Slabs
Hey there! Let’s talk about the benefits of control joints in concrete slabs. When it comes to pouring concrete, control joints play a vital role in preventing cracks and ensuring the overall durability of the structure. These joints are designed to control the cracking caused by the natural expansion and contraction of the concrete due to temperature changes and drying shrinkage.
Imagine your concrete slab as a giant chocolate bar. Just like how you score the chocolate before breaking it into pieces to control where it cracks, control joints serve a similar purpose in concrete. They provide a planned path for the concrete to crack, preventing random, unsightly cracks from forming haphazardly.
By strategically placing control joints at specific intervals, contractors can help the concrete slab maintain its integrity over time. This not only enhances the structural stability of the slab but also prolongs its lifespan. So, next time you see those neat lines on a concrete surface, you’ll know that those are more than just random grooves – they are the unsung heroes preserving the strength and appearance of the concrete slab.
In conclusion, understanding the importance of control joints in concrete slabs can make a huge difference in the longevity and performance of the structure. So, the next time you take on a concrete project, make sure to give control joints the attention they deserve. Happy building!
Factors Affecting Control Joint Placement
When it comes to deciding when to cut control joints in a concrete slab, there are several factors to consider in order to ensure the overall stability and longevity of the structure. One key consideration is the size of the slab; larger concrete slabs are more prone to cracking due to the natural expansion and contraction that occurs with changes in temperature and humidity. By strategically placing control joints at regular intervals, you can help control where the cracks form, minimizing the risk of unsightly and potentially damaging cracks.
Another important factor to think about is the thickness of the concrete slab. Thicker slabs will require more control joints to help prevent cracking, as the stress on the concrete is distributed differently than in thinner slabs. Additionally, the type of reinforcement used in the slab, such as rebar or wire mesh, can also impact when and where control joints should be placed.
These reinforcements can help strengthen the concrete and limit the size and spread of any cracks that do occur. It’s also essential to consider the overall layout and design of the concrete slab. Factors like the shape of the slab, its proximity to existing structures or trees, and the intended use of the space can all influence control joint placement.
For example, a concrete slab that will be supporting heavy equipment or vehicles may require more control joints to withstand the added pressure. Ultimately, the key is to find the right balance between too few and too many control joints. Cutting control joints at the appropriate time and in the right locations can help ensure that your concrete slab remains strong and durable for years to come.
So, next time you’re planning a concrete project, take the time to carefully consider when to cut those control joints – your slab will thank you for it in the long run!
Concrete Mix Design
Have you ever wondered why control joints are placed in concrete structures? Well, let me break it down for you. Control joint placement is crucial in ensuring the durability and longevity of concrete. Factors such as temperature changes, shrinkage, and cracking can all affect the integrity of concrete over time.
By strategically placing control joints, contractors can control where the concrete cracks, allowing for better structural integrity and preventing random cracks from forming. Think of control joints as a safety valve for concrete, allowing it to expand and contract without causing unsightly cracks. So, the next time you see those lines in a sidewalk or driveway, know that they are there for a good reason – to keep the concrete strong and crack-free.
Temperature and Weather Conditions
Hey there, let’s talk about the factors that influence control joint placement in construction projects. One crucial aspect to consider is temperature and weather conditions. These factors can greatly impact the setting and curing of concrete, which in turn affects the placement of control joints.
Think of it like trying to bake a cake on a hot, sunny day versus a cold, rainy day. The weather plays a significant role in how the cake (or in this case, the concrete) turns out. High temperatures can cause concrete to cure too quickly, leading to cracks and shrinkage, while low temperatures can slow down the curing process, affecting the strength and durability of the structure.
So, when it comes to control joint placement, it’s essential to monitor the weather forecast and adjust your construction schedule accordingly. By taking into account the temperature and weather conditions, you can ensure that the concrete sets properly and minimize the risk of cracking and other issues down the road. In conclusion, don’t underestimate the power of Mother Nature when it comes to control joint placement.
By staying mindful of the temperature and weather conditions, you can set yourself up for success in your construction projects.
Slab Thickness and Dimensions
When it comes to pouring concrete slabs, understanding the factors that affect control joint placement is crucial for a successful project. One of the key considerations is the slab thickness and dimensions. The thickness of the slab will determine how much weight it can support and how it will react to changes in temperature and moisture.
Thicker slabs are generally more durable and less prone to cracking, but they also require more materials and labor to install. The dimensions of the slab, such as length and width, will also impact where control joints should be placed to prevent cracking. Imagine building a house without a solid foundation – it would be like trying to stand on a wobbly surface! The same goes for concrete slabs; if they’re not poured correctly, they can crack and shift over time.
By considering factors like slab thickness and dimensions, you can ensure that your concrete project is built to last. So, next time you’re planning a concrete pour, think about how these factors will affect control joint placement and ultimately the longevity of your slab. It may seem like a small detail, but it can make a big difference in the quality and lifespan of your construction project.
Best Practices for Cutting Control Joints
When it comes to pouring a concrete slab, knowing when to cut control joints is crucial for preventing cracks and ensuring the longevity of your project. Control joints are designed to control where the concrete cracks, giving it room to expand and contract without damaging the slab. So, when should you cut control joints in your concrete? Well, a good rule of thumb is to make cuts at a depth of one-fourth the thickness of the slab.
This means that for a 4-inch thick slab, you should cut control joints at least 1 inch deep. But timing is also key. You want to cut control joints as soon as possible after finishing the concrete while it’s still green.
This allows for clean cuts and helps prevent random cracks from forming. If you wait too long, the concrete may already start cracking on its own, making it harder to control where the cracks occur. Additionally, cutting control joints too early can lead to raveling, where the edges of the cut break off.
Think of control joints like the lines on a coloring book – they give the concrete a designated path to follow, preventing it from straying outside the lines and creating unsightly cracks. By following best practices for cutting control joints, you’ll be setting your concrete slab up for success and ensuring a smooth finish that will stand the test of time.
Equipment and Tools Needed
When it comes to achieving precision in cutting control joints, having the right equipment and tools is key. One essential tool you’ll need is a quality concrete saw, which can come in various types such as hand-held, walk-behind, or even ride-on saws for larger projects. These saws are designed to make clean and straight cuts in the concrete, ensuring that your control joints are well-defined and effective in controlling cracking.
Additionally, having a diamond blade specifically designed for cutting concrete will make the job much easier and help you achieve smooth and precise cuts. Think of your concrete saw as a painter’s brush and the diamond blade as the paint – without the right tools, your masterpiece will lack the finesse it deserves. It’s important to also have safety gear such as goggles, gloves, and ear protection to keep yourself safe while operating the saw.
Proper safety measures not only protect you from potential harm but also ensure that you can focus on the task at hand without any distractions. Furthermore, a joint filler material is essential to seal and protect the control joints once they are cut. This material helps prevent debris from accumulating in the joints and maintains the structural integrity of the concrete over time.
By investing in high-quality tools and materials, you can ensure that your cutting control joint practices are top-notch and that your concrete projects stand the test of time. Remember, the right tools in the hands of a skilled operator can make all the difference in the outcome of your project.
Proper Spacing and Depth of Joints
Hey there, fellow DIY enthusiasts! Let’s talk about the importance of proper spacing and depth of joints when it comes to cutting control joints in your concrete projects. Picture this: you’ve just finished pouring and leveling your concrete slab, and now it’s time to think about those control joints. These joints are like the lifelines of your concrete, helping to prevent cracks and ensure its longevity.
So, what’s the deal with spacing and depth? Well, let me break it down for you. When it comes to spacing, you want to make sure that your joints are strategically placed to relieve stress and control where the cracks might occur. Too much space between joints can lead to random cracking, while too little space can cause the concrete to crack along the wrong lines.
It’s all about finding that sweet spot for optimal protection. Depth is just as crucial as spacing. Think of it like this: cutting control joints is like giving your concrete room to breathe.
By cutting deep enough, you’re allowing the concrete to naturally expand and contract without causing damage. It’s like creating a safety net for your slab, ensuring that any movement is controlled and contained within the joints. In conclusion, when it comes to cutting control joints, remember that proper spacing and depth are key.
Take the time to plan out your joints thoughtfully, considering the dimensions of your project and the environment it’s in. By following these best practices, you’ll not only prevent unsightly cracks but also protect the integrity of your concrete for years to come. Happy cutting!
Recommended Timing for Cutting Control Joints
So, you’ve just poured your concrete slab, and now you’re wondering, “When should I cut those control joints?” Well, let me break it down for you. The ideal timing for cutting control joints in a concrete slab is crucial to prevent random cracking. You want to strike a balance between cutting them too soon and risking raveling or cutting them too late and ending up with unsightly cracks.
Picture this: cutting control joints is like slicing a cake. You don’t want to cut it right out of the oven when it’s still raw, nor do you want to wait until it’s stone cold and hard as a rock. The best time to cut control joints is typically within 6 to 12 hours after finishing the concrete.
This window allows the concrete to set and firm up enough to hold the straight lines of the joints without causing any messy edges. Timing is everything when it comes to cutting control joints. If you wait too long, the concrete may have already started to crack on its own, making it harder to control where the cuts should be.
On the other hand, cutting them too early can cause the concrete to slump and deform, ruining the clean look of your slab. So, remember, when in doubt, follow the 6 to 12-hour rule for cutting control joints in your concrete slab. It’s the sweet spot that will give you the best results and help your slab stay strong and crack-free in the long run.
Early-Age Control Joint Cutting
Hey there, early-age control joint cutting is crucial for ensuring the longevity and durability of concrete structures. The recommended timing for cutting control joints is essential to prevent random cracking that can occur as the concrete cures and shrinks. Think of control joints as a way to give your concrete room to breathe.
By strategically cutting these joints at the right time, usually within the first 6 to 18 hours after the concrete is poured, you allow it to control where it wants to crack instead of leaving it to chance. It’s like giving your concrete a roadmap to follow, guiding it along the path of least resistance. Cutting control joints at the optimal time can also enhance the overall aesthetics of the concrete, preventing unsightly random cracks from marring the surface.
Plus, it helps maintain the structural integrity of the concrete, ensuring it can withstand the test of time. So, next time you’re pouring concrete, remember the importance of early-age control joint cutting and make sure to follow the recommended timing for cutting control joints. Your concrete will thank you for it in the long run!
Drying and Curing Period
When it comes to concrete work, the drying and curing period is crucial for ensuring a strong and durable final product. One important aspect of this process is knowing the recommended timing for cutting control joints. These control joints help prevent cracking by allowing the concrete to expand and contract without causing damage.
But when should you make these cuts? Ideally, control joints should be cut into the concrete soon after it has been poured and before it has completely hardened. This is usually done within the first 6 to 18 hours, depending on the specific mix and environmental conditions. Cutting control joints at the right time ensures that they are effective in controlling cracking while also maintaining the structural integrity of the concrete.
Imagine trying to slice a cake after it has been sitting out for too long – it crumbles and doesn’t look as neat. The same concept applies to cutting control joints in concrete. If you wait too long, the concrete can become too hard and prone to cracking along unintended paths.
So, timing is key when it comes to cutting control joints. By following the recommended guidelines and making these cuts at the right time, you can help ensure that your concrete project stays strong and crack-free for years to come. It may seem like a small detail, but it can make a big difference in the overall quality and longevity of your concrete work.
Preventing Random Cracks
Have you ever noticed random cracks appearing in your concrete projects, ruining all your hard work? It’s frustrating, right? Well, the good news is that you can prevent those pesky cracks by using control joints. But timing is key! When should you cut control joints to ensure your concrete stays crack-free for longer? The recommended timing for cutting control joints is crucial for the success of your project. Imagine control joints as the seams on a piece of clothing.
Just like seams allow fabric to expand and contract without tearing, control joints in concrete give it room to move without cracking. So, cutting control joints at the right time is like finding the perfect fit for your concrete – it allows for natural expansion and contraction without causing unsightly cracks. So, when is the best time to cut control joints? Typically, it’s best to do it within the first 12 hours of finishing the concrete while it’s still green.
This timing allows the concrete to be cut easily without chipping or causing fractures. Cutting control joints at the recommended time ensures that your concrete will stay looking smooth and crack-free for years to come. So, don’t skip this important step in your concrete projects – your future self will thank you!
Conclusion
In conclusion, cutting control joints in a concrete slab is like giving the concrete room to breathe and stretch without cracking under pressure. It’s like creating a roadmap for the concrete to follow, ensuring it stays smooth and even in the long run. So, remember, when it comes to concrete slabs, timing is key – cutting control joints at the right time will keep your project on the straight and narrow path to success!”
FAQs
What is the purpose of control joints in a concrete slab?
Control joints are used in concrete slabs to control cracking caused by shrinkage during the curing process.
When should control joints be cut in a concrete slab?
Control joints should be cut as soon as the concrete is hard enough to prevent raveling but before random cracks appear.
How deep should control joints be cut in a concrete slab?
Control joints should be cut to a depth of one-fourth the slab thickness for optimal crack control.
What tools are commonly used to cut control joints in a concrete slab?
Tools such as a concrete saw, joint cutter, or grooving tool are commonly used to cut control joints in a concrete slab.
How far apart should control joints be spaced in a concrete slab?
Control joints should be spaced at regular intervals, typically 24 to 36 times the thickness of the slab.
Can control joints be added to an existing concrete slab?
Yes, control joints can be added to an existing slab by cutting or routing grooves to help control cracking.
What are the benefits of cutting control joints in a concrete slab?
Cutting control joints helps to prevent random cracking, reduce the likelihood of heaving or settling, and improve the overall durability of the concrete slab.